Manufacturing Bankrupt Business : 5 Remarkable Opportunities
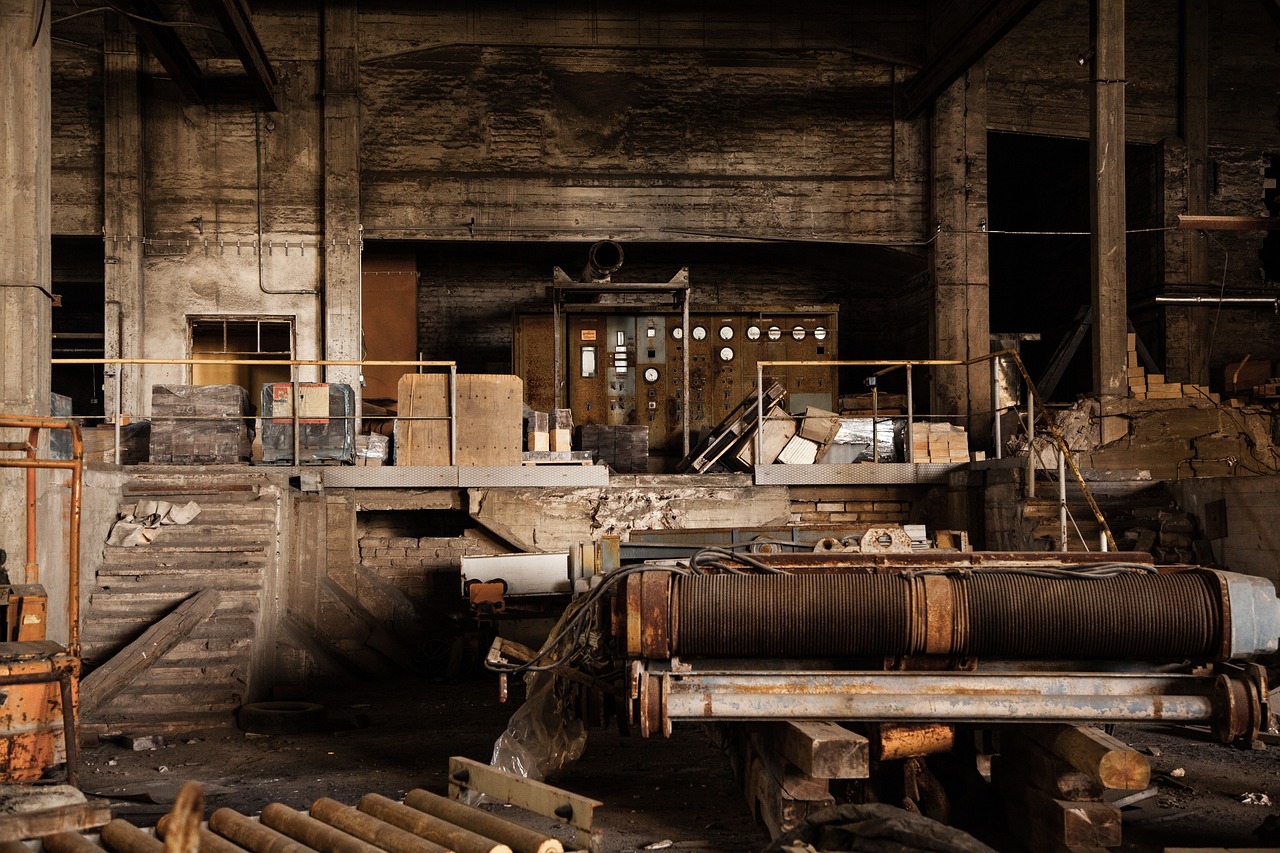
In the complex landscape of modern industry, manufacturing businesses face a myriad of challenges “Manufacturing Bankrupt Business”.
Among these, the looming threat of bankruptcy casts a long shadow, affecting not only individual companies but also entire economies. Understanding the nuanced interplay of factors leading to bankruptcy is crucial for stakeholders across the manufacturing sector.
From identifying early warning signs to implementing strategic measures for recovery, this article delves into the intricacies of “Manufacturing Bankrupt Business.” By examining key elements such as financial dynamics,
market forces, and innovative strategies, we aim to equip readers with actionable insights to navigate the turbulent waters of the manufacturing world. Join us as we explore the path towards resilience and success in the face of adversity.
Understanding the Dynamics of Manufacturing Bankrupt Business
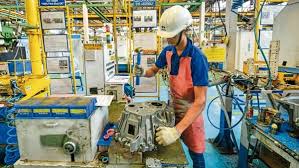
The manufacturing industry serves as the backbone of economies worldwide, encompassing a vast array of sectors from automotive and electronics to pharmaceuticals and consumer goods. Understanding the intricate dynamics of this sector is paramount to grasping the complexities that underlie the phenomenon of businesses facing bankruptcy.
Evolution of Manufacturing: The manufacturing landscape has undergone significant transformations over the years, driven by advancements in technology, globalization, and shifting consumer demands. Traditional manufacturing methods have given way to automation, robotics, and digitalization, revolutionizing production processes and supply chains.
Economic Significance: Manufacturing plays a pivotal role in driving economic growth, job creation, and innovation. It forms the backbone of industrial economies, fostering productivity and driving competitiveness on both domestic and global scales.
Supply Chain Dynamics: The manufacturing industry operates within intricate supply chain networks, linking raw material suppliers, manufacturers, distributors, and retailers. Any disruption or inefficiency within these chains can have cascading effects, impacting production schedules, inventory management, and ultimately, financial stability.
Competitive Pressures: In an increasingly competitive marketplace, manufacturing businesses face relentless pressures to innovate, optimize efficiency, and deliver products at competitive prices. This intense competition, coupled with volatile market conditions, exacerbates the risk of financial distress and bankruptcy.
Technological Advancements: The advent of Industry 4.0 technologies, including artificial intelligence, internet of things (IoT), and big data analytics, has revolutionized the manufacturing landscape. While these innovations offer unprecedented opportunities for efficiency and productivity gains, they also introduce new complexities and challenges that must be navigated adeptly.
Globalization and Trade Dynamics: The globalization of supply chains and trade networks has created both opportunities and vulnerabilities for manufacturing businesses. While access to global markets facilitates growth and expansion, it also exposes businesses to geopolitical risks, currency fluctuations, and trade barriers that can disrupt operations and erode profitability.
Regulatory Environment: Manufacturing businesses operate within a complex regulatory framework, encompassing labor laws, environmental regulations, safety standards, and trade policies. Compliance with these regulations is not only a legal requirement but also a critical component of risk management and corporate governance.
Sustainability and Social Responsibility: In an era of increasing environmental awareness and social consciousness, manufacturing businesses are under mounting pressure to adopt sustainable practices and demonstrate corporate social responsibility. Failure to address these concerns not only jeopardizes reputation and brand integrity but also exposes businesses to regulatory scrutiny and consumer backlash.
Identifying Early Warning Signs of Financial Distress
Recognizing the early warning signs of financial distress is paramount for manufacturing businesses to proactively address underlying issues and mitigate the risk of bankruptcy. By closely monitoring key indicators and implementing timely interventions, businesses can enhance their resilience and safeguard their long-term viability.
Declining Profit Margins: One of the most telling indicators of financial distress in manufacturing businesses is a sustained decline in profit margins. Shrinking margins may result from various factors, including rising production costs, pricing pressures, and declining demand for products or services. Monitoring gross profit margins and identifying deviations from historical trends can provide valuable insights into the financial health of the business.
Cash Flow Challenges: Cash flow is the lifeblood of any manufacturing operation, fueling day-to-day operations, investment activities, and debt servicing obligations. A persistent shortage of cash or deteriorating cash flow metrics, such as increasing accounts receivable days or declining cash reserves, may signal underlying liquidity issues and impending financial distress. Proactive cash flow management and forecasting are essential to mitigate cash flow challenges and ensure solvency.
Rising Debt Levels: Excessive debt levels can burden manufacturing businesses with high interest payments, restrict financial flexibility, and increase the risk of default. Monitoring key debt metrics, such as debt-to-equity ratio, interest coverage ratio, and debt service coverage ratio, can help identify unsustainable debt levels and potential liquidity constraints. Taking proactive measures to deleverage the balance sheet and refinance expensive debt can alleviate financial strain and enhance financial stability.
Inventory Management Issues: Inefficient inventory management practices can tie up valuable working capital, increase carrying costs, and expose manufacturing businesses to inventory obsolescence risks. Excessive inventory levels, slow inventory turnover rates, and frequent stockouts may indicate underlying operational inefficiencies and supply chain disruptions. Implementing inventory optimization strategies, adopting just-in-time inventory management techniques, and leveraging data analytics can improve inventory visibility, reduce carrying costs, and enhance operational efficiency.
Customer Concentration Risks: Overreliance on a small number of customers or a single market segment can expose manufacturing businesses to significant revenue concentration risks. A loss of a major customer or a downturn in a key market can have profound implications for revenue stability and profitability. Diversifying the customer base, expanding into new markets, and cultivating long-term customer relationships can mitigate customer concentration risks and enhance business resilience.
Regulatory Compliance Issues: Non-compliance with regulatory requirements can subject manufacturing businesses to legal penalties, regulatory sanctions, and reputational damage. Failure to adhere to environmental regulations, safety standards, and labor laws can result in fines, litigation costs, and operational disruptions. Implementing robust compliance programs, conducting regular audits, and staying abreast of regulatory developments can mitigate regulatory compliance risks and safeguard corporate reputation.
Factors Contributing to Manufacturing Bankrupt Business
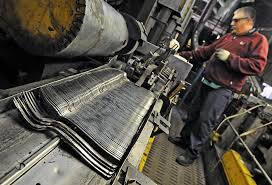
Bankruptcy in manufacturing businesses can stem from a multitude of factors, ranging from internal operational challenges to external market forces. Understanding these contributing factors is essential for stakeholders to develop effective strategies for risk mitigation and financial stability.
Economic Downturns: Manufacturing businesses are particularly vulnerable to economic downturns and cyclical fluctuations in demand. During periods of recession or economic slowdown, consumer spending contracts, industrial activity declines, and business investment diminishes, leading to reduced demand for manufactured goods and services. The resulting decline in sales revenues and profitability can strain cash flow, impair liquidity, and exacerbate financial distress, ultimately culminating in bankruptcy.
Cost Overruns and Operational Inefficiencies: Cost overruns and operational inefficiencies can erode profit margins, constrain cash flow, and undermine the financial viability of manufacturing businesses. Inadequate cost control measures, inefficient production processes, and supply chain disruptions can contribute to escalating production costs, prolonged lead times, and suboptimal resource utilization. Addressing root causes of cost overruns, streamlining operational workflows, and implementing lean manufacturing principles can enhance operational efficiency and mitigate financial risk.
Technological Disruptions: Rapid technological advancements and disruptive innovations can render existing manufacturing processes, products, and business models obsolete, posing existential threats to incumbent players. Failure to embrace emerging technologies, adapt to changing market dynamics, and innovate competitively can leave manufacturing businesses vulnerable to competitive pressures and market disruption. Investing in research and development, fostering a culture of innovation, and embracing digital transformation initiatives can enable manufacturing businesses to stay ahead of the curve and sustain long-term competitiveness.
Supply Chain Disruptions: Manufacturing businesses operate within intricate supply chain ecosystems, spanning multiple suppliers, vendors, and partners across global markets. Disruptions to the supply chain, such as natural disasters, geopolitical conflicts, trade disputes, and transportation bottlenecks, can disrupt production schedules, impair inventory management, and impede order fulfillment. Implementing supply chain resilience strategies, diversifying sourcing options, and establishing contingency plans can mitigate supply chain risks and enhance business continuity.
Intense Competition and Pricing Pressures: The manufacturing industry is characterized by intense competition and pricing pressures, driven by globalization, market saturation, and commoditization of products and services. Price competition, margin erosion, and aggressive pricing tactics can exert downward pressure on profitability, erode market share, and compromise financial sustainability. Differentiating products through innovation, enhancing value proposition, and pursuing niche market segments can mitigate competitive pressures and sustain pricing power.
Regulatory Compliance Costs: Manufacturing businesses are subject to a myriad of regulatory requirements, encompassing environmental regulations, safety standards, labor laws, and product quality standards. Compliance with regulatory mandates entails substantial costs, including investments in pollution control measures, workplace safety enhancements, regulatory reporting, and legal compliance. Failure to comply with regulatory requirements can result in fines, penalties, litigation costs, and reputational damage, jeopardizing financial stability and viability.
Impact of Market Fluctuations on Manufacturing Sector
Market fluctuations exert a profound influence on the performance and stability of manufacturing businesses. Understanding the nature and implications of these fluctuations is essential for stakeholders to navigate dynamic market conditions and mitigate financial risks effectively.
Demand Volatility: The manufacturing sector is highly sensitive to fluctuations in demand, which can stem from changes in consumer preferences, economic cycles, and geopolitical factors. Volatility in demand can lead to erratic production schedules, inventory imbalances, and revenue fluctuations, challenging manufacturers to adapt swiftly to changing market dynamics. Implementing demand forecasting models, maintaining agile production capabilities, and fostering flexibility in supply chain operations can help manufacturing businesses mitigate the impact of demand volatility and optimize resource allocation.
Currency Exchange Rates: Manufacturing businesses with international operations are exposed to currency exchange rate fluctuations, which can impact the competitiveness of exported goods, production costs, and revenue streams. Appreciation or depreciation of the domestic currency relative to foreign currencies can affect export competitiveness, profit margins, and cash flow dynamics. Employing hedging strategies, diversifying currency exposure, and optimizing pricing strategies can help mitigate currency exchange rate risks and enhance financial stability in volatile currency markets.
Commodity Price Volatility: Manufacturing businesses reliant on raw materials and commodities are susceptible to price volatility in global commodity markets. Fluctuations in commodity prices, driven by supply-demand dynamics, geopolitical tensions, and macroeconomic factors, can impact production costs, profit margins, and inventory valuation. Developing strategic supplier relationships, implementing inventory management practices, and exploring alternative sourcing options can mitigate commodity price volatility risks and enhance cost competitiveness.
Regulatory Changes and Trade Policies: Changes in regulatory frameworks and trade policies can introduce uncertainty and disrupt manufacturing supply chains and market access. Shifting regulatory requirements, tariffs, trade barriers, and geopolitical tensions can impact import-export dynamics, supply chain configurations, and market entry strategies. Monitoring regulatory developments, conducting scenario analysis, and engaging in advocacy efforts can help manufacturing businesses anticipate regulatory changes and navigate evolving trade landscapes effectively.
Technological Disruptions and Industry Trends: Technological advancements and industry trends can drive disruptive changes in manufacturing processes, business models, and consumer preferences. Emerging technologies, such as artificial intelligence, additive manufacturing, and automation, are reshaping production methods, enhancing operational efficiency, and creating new market opportunities. Embracing innovation, investing in technology adoption, and fostering a culture of continuous learning can enable manufacturing businesses to stay ahead of the curve and capitalize on emerging trends in the industry.
Geopolitical Risks and Global Events: Geopolitical tensions, geopolitical risks, and global events can introduce uncertainty and volatility into the manufacturing landscape, affecting supply chain operations, market access, and business investments. Political instability, trade disputes, natural disasters, and public health crises can disrupt global trade flows, supply chain networks, and consumer confidence, posing challenges for manufacturing businesses operating in interconnected global markets. Developing risk management frameworks, diversifying supply chain dependencies, and enhancing business resilience can mitigate geopolitical risks and enhance adaptive capacity in the face of global uncertainties.
Strategies for Sustainable Cost Management
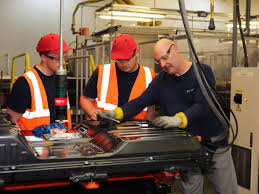
Effective cost management is essential for maintaining competitiveness, maximizing profitability, and ensuring long-term sustainability in the manufacturing sector. Implementing strategic cost management initiatives enables manufacturing businesses to optimize resource allocation, streamline operations, and adapt to changing market dynamics efficiently.
Cost Analysis and Cost Drivers: Conducting comprehensive cost analysis is the foundation of effective cost management. Identifying cost drivers, including raw materials, labor, overheads, and production processes, enables manufacturing businesses to understand the factors contributing to overall costs and prioritize cost reduction efforts. Leveraging cost accounting techniques, such as activity-based costing and variance analysis, facilitates accurate cost allocation and informed decision-making.
Lean Manufacturing Principles: Adopting lean manufacturing principles is instrumental in eliminating waste, enhancing efficiency, and reducing costs across the production process. Lean methodologies, such as value stream mapping, 5S workplace organization, and continuous improvement (kaizen), empower manufacturing businesses to streamline workflows, minimize inventory levels, and optimize resource utilization. Embracing a culture of continuous improvement fosters innovation, drives operational excellence, and promotes cost-conscious behavior throughout the organization.
Supplier Relationship Management: Developing strategic relationships with suppliers is integral to cost management and supply chain optimization. Collaborating closely with suppliers, negotiating favorable terms, and implementing vendor management strategies enable manufacturing businesses to secure competitive pricing, minimize procurement costs, and mitigate supply chain risks. Building resilient supplier networks, diversifying sourcing options, and fostering long-term partnerships enhance supply chain agility and reduce dependency on single suppliers.
Product Lifecycle Management: Implementing effective product lifecycle management (PLM) practices enables manufacturing businesses to optimize product development processes, reduce time-to-market, and minimize costs throughout the product lifecycle. From design and prototyping to manufacturing and distribution, PLM solutions facilitate collaboration, streamline workflows, and ensure alignment with customer requirements and market demands. Integrating PLM systems with enterprise resource planning (ERP) platforms enhances visibility, traceability, and control over product lifecycle processes, driving efficiency and reducing costs.
Operational Efficiency Improvements: Enhancing operational efficiency is central to cost management in manufacturing businesses. Implementing process optimization initiatives, standardizing operating procedures, and deploying advanced manufacturing technologies enable businesses to improve productivity, reduce cycle times, and minimize resource wastage. Investing in automation, robotics, and digitalization streamlines repetitive tasks, eliminates manual errors, and enhances production flexibility, driving cost savings and enhancing competitive advantage.
Value Engineering and Cost-Effective Design: Adopting value engineering principles and cost-effective design strategies enable manufacturing businesses to optimize product performance, functionality, and cost competitiveness. Collaborating cross-functionally with engineering, design, and procurement teams facilitates the identification of cost-saving opportunities, material substitutions, and design optimizations without compromising product quality or customer satisfaction. Balancing cost considerations with performance requirements and market expectations ensures that products remain competitive and profitable throughout their lifecycle.
Continuous Cost Monitoring and Improvement: Sustaining cost management efforts requires ongoing monitoring, analysis, and refinement of cost reduction initiatives. Establishing key performance indicators (KPIs), conducting regular cost reviews, and benchmarking against industry peers enable manufacturing businesses to track progress, identify performance gaps, and adjust strategies accordingly. Encouraging employee engagement, empowering frontline workers, and soliciting feedback fosters a culture of cost consciousness and continuous improvement across the organization.
Importance of Diversification in Manufacturing Operations
Diversification is a strategic imperative for manufacturing businesses seeking to mitigate risks, capitalize on new opportunities, and achieve sustainable growth in dynamic and competitive markets. By expanding product offerings, customer segments, and geographical markets, manufacturing businesses can enhance resilience, reduce dependency on specific revenue streams, and position themselves for long-term success.
Product Diversification: Diversifying product offerings enables manufacturing businesses to cater to diverse customer needs, mitigate concentration risks, and capitalize on emerging market trends. Introducing new product lines, variants, and customization options expands market reach, drives revenue growth, and enhances competitive differentiation. Conducting market research, analyzing consumer preferences, and leveraging customer feedback inform product diversification strategies and ensure alignment with market demands.
Market Diversification: Expanding into new geographical markets diversifies revenue streams, reduces exposure to regional economic fluctuations, and mitigates geopolitical risks. Identifying growth opportunities in untapped markets, establishing local partnerships, and adapting marketing strategies to cultural nuances facilitate market entry and expansion. Balancing market diversification with localization initiatives, regulatory compliance, and supply chain resilience enhances market penetration and sustains long-term growth across diverse markets.
Customer Diversification: Diversifying customer segments minimizes dependency on individual customers or market segments and reduces vulnerability to customer-specific risks, such as changes in buying behavior or competitive pressures. Targeting diverse customer demographics, industries, and distribution channels expands customer reach, fosters customer loyalty, and mitigates revenue concentration risks. Developing tailored value propositions, nurturing strategic partnerships, and delivering exceptional customer experiences strengthen relationships and drive customer retention across diverse segments.
Supply Chain Diversification: Diversifying supply chain sources and dependencies mitigates risks associated with supplier disruptions, geopolitical tensions, and natural disasters. Cultivating relationships with multiple suppliers, sourcing from alternative regions, and maintaining strategic buffer stocks enhance supply chain resilience and ensure continuity of operations. Implementing robust supplier qualification processes, conducting risk assessments, and monitoring supplier performance foster transparency, accountability, and reliability within the supply chain ecosystem.
Technology Diversification: Investing in diverse technologies and innovation initiatives enables manufacturing businesses to adapt to evolving market trends, enhance product competitiveness, and drive operational efficiency. Embracing emerging technologies, such as additive manufacturing, artificial intelligence, and internet of things (IoT), expands technological capabilities, unlocks new revenue streams, and fosters industry leadership. Collaborating with technology partners, fostering a culture of experimentation, and allocating resources to research and development initiatives drive innovation and sustain competitive advantage in dynamic markets.
Risk Management and Resilience: Diversification serves as a foundational principle of risk management, enabling manufacturing businesses to spread risks across multiple dimensions and minimize exposure to single points of failure. Proactively identifying, assessing, and mitigating risks across product, market, customer, supply chain, and technology dimensions enhances business resilience and safeguards against adverse events. Integrating risk management practices into strategic planning processes, scenario analysis, and contingency planning empowers businesses to navigate uncertainty and capitalize on opportunities in volatile environments.
Manufacturing Bankrupt Business Conclusion
In today’s volatile and competitive landscape, manufacturing businesses face numerous challenges and opportunities. Navigating market fluctuations, cost pressures, and technological advancements requires strategic thinking and adaptability. By understanding industry dynamics, recognizing financial distress signals early, and implementing proactive cost management and diversification strategies, businesses can strengthen their resilience and position themselves for long-term success. Adaptability, agility, and a commitment to excellence will be crucial as the sector evolves. Embracing change, fostering innovation, and leveraging expertise will help businesses thrive in this dynamic marketplace.
Leave a Reply
You must be logged in to post a comment.